rethink sustainability
Can plastic-eating enzymes solve the recycling problem?
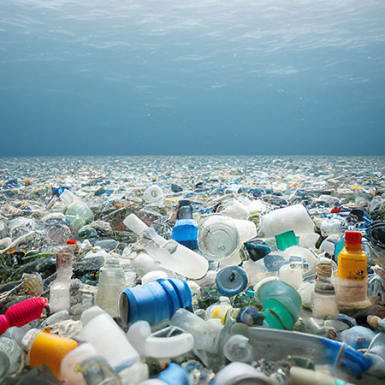
Less than 10 per cent of plastic is currently reused, but a new technology is set to create a more circular economy.
The invention of the first man-made plastic, celluloid, in the nineteenth century was hailed as revolutionary. With the discovery came a seemingly infinite conveyor-belt of products, newly affordable to the average consumer. No industry was left untouched by this cheap, malleable, bountiful resource.
Today – as plastic clogs our oceans, flows from landfills and sends plumes of smoke into the atmosphere in the rush to burn it –attitudes are a little different.
Since the first factories started pumping out polyester in the 1950s, an estimated 12.3bn tonnes of plastic has been produced as of 20241. But, of the 400mn tonnes of plastic waste produced approximately every year, less than 10 per cent is recycled2. The rest ends up in landfills, waste incinerators or nature. Microplastics have been found in penguins, breast milk, bottled water, human blood, and on the summit of Mount Everest. Most plastic will never decompose.
Read also: What are our top tips to reduce plastic pollution?
Even recycled plastic is eventually destined for the dump. Conventional, mechanical recycling –where plastic is ground into flakes, melted, and moulded anew –yields plastic more brittle and less durable than its originator. It is often difficult to use the material more than three times.
Scientists have spent decades grappling with this plastic predicament. In recent years, an unlikely ally has emerged: plastic-munching microorganisms.
Carbios, a French biotechnology start-up, is among the innovators looking to commercialise depolymerisation –or enzymatic –recycling. This uses genetically-modified microorganisms to break down the polymer chains that make up plastic, leaving only its initial building-blocks, or monomers. The monomers can then be put back together into plastic that’s as good as new. In theory, a bottle made this way could be recycled indefinitely.
According to Carbios today they are able to recycle any kind of PET [polyethylene terephthalate] plastic: bottles, food packaging, t-shirts. “The main difference with Carbios is circularity. If you buy a recycled bottle made with mechanical processes, it will be waste after a few re-uses. With one tonne of plastic, we produce 97 per cent plastic components. And we can do 30 to 50 cycles where conventional [recycling] does three to five.”
Engineering a commercially-viable enzyme has been no small feat. When Carbios began working on the recycling process back in 2011, the enzymes would destabilise in the reactors’ high temperatures and take weeks to process just a small amount of PET. It took until 2020 for Carbios to develop an enzyme –cutinase –that could withstand higher temperatures and convert a batch of PET in hours.
With that breakthrough came the first real indicator that enzymatic recycling could be rolled out at scale. In the months that followed, Carbios’ stock price soared.
Read also: From landfill to a new life: dealing with wind turbines' little-known problem
Carbios claims that its approach is less energy intensive and has a smaller carbon footprint than producing virgin PET, calculating that they can achieve CO2 emission savings of up to 46 per cent compared with virgin PET production, when taking into account the diversion of PET waste from possible incineration.
However, not all the maths adds up – it is still cheaper to produce petroleum-based plastics. The company is confident, though, that the numbers are moving in the right direction. “Global regulations are pushing brands to use more recycling content. “Then you have the commitments. Take any big brand – Nike, Puma, Pepsi –all have made pledges. When you add regulations to brand commitments, the market is there.”
There has been a global shift in governmental policy on plastic. In 2022, India banned single-use plastics, and earlier this year, Thailand banned the importation of plastic waste3. China is ramping up its biodegradable plastic production. The EU, UK and various US states have all implemented plastic regulations in the past few years.
Carbios has been busy capitalising on this “age of commitments”. It has already partnered with bottling and cosmetics giants Nestlé Waters, PepsiCo and L’Oreal, and recently signed deals with clothing brands Patagonia, Puma and Salomon. These collaborations both validate the tech and bring industry giants on board, speeding scalability and reach.
Carbios regards the latest partnerships as central to its plans for textile recycling. “The main cost in this industry is waste, and as we’re targeting waste that other recyclers can’t process [textiles] that’s a huge cost-competitive advantage for us. “A tonne of textile waste [costs] about USD 200-300, while a tonne of bottles can be USD 2,000.”
In 2021, Carbios unveiled an industrial demonstration plant in France. The company has announced plans to open its first 50,000 tonne biorecycling plant, capable of processing 2 billion bottles or 300 million t-shirts. From there, it hopes to sell licences for its technology “to get to market and global impact as fast as possible.”
But Carbios doesn’t have all the answers – yet. PET accounts for only 11 per cent of plastic waste4, and other plastic types have proved more difficult to digest.
“Our food packaging is such a bad mixture of plastic,” says Lars Blank, a professor of microbiology at Aachen University, who set up a consortium of researchers to study plastic-eating enzymes in 2015. “Food packaging has three, four, up to twelve layers of different plastics. And this is really the challenge –but also the opportunity.”
Blank, like most in the field, calls for standardised and streamlined packaging to aid recycling efforts – a simple paper label on a plastic bottle renders it unrecyclable.
Read also: Can recycling stop the retail waste crisis?
With a team of European and Chinese researchers, Blank has been developing bio-based plastics with bio-recyclable qualities. “Where Carbios degrades and purifies it and produces new PET, we’re feeding it to microbes,” says Blank. The microbes gobble up the plastic monomers, “and with the solid matter that is left over at the end, we will then look to see if we can extract other valuable substances through chemical processes or bioprocess engineering methods.”
John McGeehan, a professor of biological sciences at Portsmouth University, has also been working to develop enzymes that are faster, scalable, and able to tackle trickier waste, and which, like Carbios’ enzyme cutinase, will break waste down into its initial monomers for use as building blocks for new plastics. Research suggests there will be enzymes capable of digesting polyethylene (plastic bags) and polypropylene (hard plastics).
Like Carbios, McGeehan believes getting industry players involved is integral. “If you look at some of the big bottle manufacturers, that scale is huge. If we are able to divert some of that [thermoplastic] to the recycling part, that would be great for all of us.”
All are unanimous on the greatest current barrier to doing more: poor collection and recycling practices. According to Carbios, “collection rates have to improve. Waste is critical in this industry. If you want recycling technologies to succeed, you need to ensure more waste is collected.”
Read also: Cracking the plastic crisis?
Better collection is not the only remaining piece of the recycling puzzle, though. Fast and effective sorting is essential to increasing recycling rates – both mechanical and enzymatic recycling processes depend on clean, well-separated stock. Wider re-use of plastic products – especially packaging – will also be important, so that the environmental impact of the recycling process can be kept to a minimum. If the other pieces of the puzzle do slot into place, though, enzymatic recycling has the potential to create a truly circular plastic economy.
1 Global plastic production with projections, 1950 to 2060 | Our World in Data
2 Beat Plastic Pollution | UN Environment Programme
3 Thailand bans imports of plastic waste to curb toxic pollution | Waste | The Guardian
4 Primary plastic waste generation by polymer, 2015 (ourworldindata.org)
Important information
This document is issued by Bank Lombard Odier & Co Ltd or an entity of the Group (hereinafter “Lombard Odier”). It is not intended for distribution, publication, or use in any jurisdiction where such distribution, publication, or use would be unlawful, nor is it aimed at any person or entity to whom it would be unlawful to address such a document. This document was not prepared by the Financial Research Department of Lombard Odier.
Read more.
share.