FT Rethink
Cracking the plastic crisis?
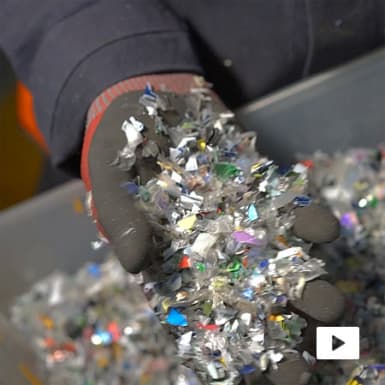
Of the 8.3 billion tonnes of plastic that has ever been made, 6.3 billion tonnes has ended up as waste—just 9% of which has been recycled. And since plastic takes over 400 years to degrade, most of the rest still exists. With another 12% having been incinerated, the other 79% has simply been discarded1. That’s almost 5 billion tonnes of plastic: the equivalent of a sheet of cling film large enough to wrap our entire planet2. Even today, only fourteen percent3 of plastic waste is recycled. The rest is buried, burned, sent to low- and middle-income countries or lost to pollute land and sea.
Now, a new industry is emerging that has the potential to turn plastic waste into a valuable resource. This industry is based on a process called chemical recycling, which breaks plastics back down into base chemicals that can then be used to make new products. This kind of theoretically endless cycle of processing and reuse is known as a circular economy.
A significant part of the problem of plastic waste is due to the overproduction of plastic goods, such as single-use packaging. And since production is responsive to consumer demand, changing our own behaviours so that we use less and re-use more plastic is an important part of the puzzle. Such solutions are classified as ‘upstream’, as opposed to ‘downstream” solutions like recycling. That said, such changes tend to happen slowly, and so we cannot rely on a shift in consumer demand to solve the problem any time soon. Indeed, on our current trajectory, the amount of plastic waste entering our oceans is expected to triple over the next 20 years4.
Increasing the amount of plastic we recycle, then, is vital to solving the plastic emergency. However, some plastics cannot be easily recycled using traditional mechanical methods—which is where chemical recycling can play an important role.
This process isn’t without its limitations. Chemical recycling is a young technology that requires a lot of energy, and we aren’t yet in a position to fully understand its potential contributions and impacts—both positive and negative. Moreover, an analysis by the Pew Charitable Trusts suggests that chemical recycling can only reclaim around 6% of plastic waste by 20404.
However, even if this modest forecast is accurate, chemical recycling would still enable us to recycle over 25 million tonnes of plastic waste every year. So, although the process cannot tackle the plastic crisis by itself, chemical recycling still has the potential to be an important part of the solution by diverting that plastic away from landfills and incineration, where 50% of the EU’s plastic waste still ends up5. Backers claim that the process can enable us to expand the range of plastic recycling beyond what mechanical methods are capable of handling to include plastics such as mixed polymers, low-value & contaminated plastics and pigments. Chemical recycling can also produce higher-quality materials than conventional recovery methods.
Plastic pollution doesn't just come from obvious sources like bags and bottles. Many other products are also significant sources of plastic waste, such as coffee cups, disposable wipes and even glitter. In the UK, one of a new breed of businesses testing chemical recycling technology for commercial operations is targeting one of these lesser-known sources of plastic waste: used tyres, which are typically 24% plastic. Created by two friends who met at university, Big Atom Advanced Recycling has built an imposing mechanical plant in the petrochemical hub of Merseyside, where conveyor belts and ferocious-looking steel-bladed teeth shred and separate the rubber, metal and textiles from one tonne of tyres every hour. Big Atom estimates that chemical recycling could save two tonnes of CO2 emissions for every tonne of rubber and plastics the company processes.
After testing on a small-scale laboratory rig, Big Atom has just taken delivery of a much larger reactor that will break down tyre rubber into basic hydrocarbons by heating it in the absence of oxygen—a thermochemical process called pyrolysis. A distillation process is then used to convert these hydrocarbons into useful output products ranging from heavier waxes and oils to lighter oils and gasses, depending on the durations and temperatures used6.
The company’s founders claim to have developed a method that uses lower temperatures to save energy, as well as using some of the output gasses to generate electricity to power the reactor. “This is a chemical process—the bread and butter of what it is to be a chemical engineer,” says co-founder Toby Moss. “My background in oil and gas has helped us optimise this process to be more value-producing and environmentally beneficial.”
Refining the mechanical process that pulverises old rubber and separates it into different elements is critical. “For the pyrolysis process to work efficiently and in a way that gives us control over the output products, we first need to have good control of the stock that we feed into the reactor,” explains co-founder Alex Guslisty.
The chemical part of Big Atom’s recycling process is still in development. For now, the rubber extracted from old tyres is sold on for re-use in products like soft surfacing for sports and playgrounds. But after further testing and tinkering to prove the viability and efficiency of the process and reactor design, Moss is confident that the company can begin commercial chemical recycling operations by the end of 2021. This will enable Big Atom to begin feeding recycled oil back into refineries that will use it to make new plastic goods in place of virgin crude oil—an economical and, crucially, environmentally sustainable alternative that will contribute to reducing plastic waste and limiting the overall amount of plastic in existence.
“We need to see more sites trialling this technology, better infrastructure in the refining industry and greater demand for circular products,” Alex Guslisty explains. “These are the things that will really help this market to grow and for us to process all of our rubber and plastic waste here in the UK, instead of sending it abroad.”
Like most developed nations, the UK produces more plastic waste than it can process and sends much of it overseas. Between 2010 and 2016, China alone imported between seven and nine million tonnes of plastic waste a year7. Since China banned the trade in 2018, the problem has shifted to countries in Southeast Asia such as Indonesia, Thailand and Vietnam8.
For Adrian Griffiths, CEO and founder of another fledgling UK chemical recycling business—Swindon-based Recycling Technologies—this is simply unacceptable. “I think it’s a travesty that, in a modern society, we actually call things recycled simply because we’ve put them on a ship and sent them overseas,” says Griffiths. “Some of that plastic will undoubtedly get recycled, but the sad reality is that a lot of it doesn’t and is, therefore, creating a problem for those countries. Any civilised society should have to deal with its waste within the confines of its own borders.”
As of this year, the EU has banned the export of plastic waste to countries that do not have the same sustainability goals or capacity for large-scale recycling9. The goal is, where possible, to keep plastic waste within the EU and the borders of its country of origin to avoid sending it to landfills or incinerators. However, the problem of efficiently recycling this waste remains.
To address that challenge, Griffiths has used his experience as a former automotive engineer to create a commercial plant with a modular design that makes it relatively easy to transport and assemble anywhere in the world. The machine processes films and laminated plastics—such as crisp packets and yoghurt pots—using another version of the pyrolytic process to break them down into a variety of waxes, oils and gasses.
While some of these output products could be burned to create energy, the process is a significant source of greenhouse gas emissions. Instead, Griffiths is adamant that the future of chemical recycling lies in producing raw materials for new products. “What we really want to do is take these materials back to the petrochemical industry and use them as the feedstock for making more plastic,” explains Griffiths. “The world has to get out of the habit of burning anything with carbon in it, and so we want to make sure that chemically recycled plastic isn’t just used for fuel.”
Though still in its infancy, the widespread use of chemical recycling has the potential to reduce the amount of discarded plastic that ends up buried, incinerated or littering the world’s oceans. Big chemical manufacturers like BASF, Sabic and Total are already throwing their weight behind chemical recycling initiatives. Meanwhile, many investors are betting on start-ups in this nascent field. In the US alone, USD 4.3 billion has been invested into projects aiming to convert plastic waste into new polymers or fuel since 201710. These developments coincide with pledges by big consumer goods brands to slash the amount of “virgin” plastics— those that have not been processed before—in their packaging.
However, if chemical recycling is to make a serious dent in the estimated 350 million tonnes of plastic churned out globally each year11, it will need to prove competitive during times of low crude oil and natural gas prices that make virgin plastics cheaper to produce. Regulation and taxes on virgin plastics, such as the one introduced by the UK Government last year12, would also provide important incentives for industries to embrace recycled plastics.
Despite all the potential benefits of chemical recycling, doubters remain. With the petrochemicals industry planning to invest USD 400 billion in new capacity over the next five years13, some campaigners view these novel waste treatments as a distraction from the root of the problem: overproduction of packaging and the consumer demand that feeds it.
But while public awareness of the problem continues to grow, plastic pollution is an urgent challenge that cannot wait for the slow-moving tide of consumer attitudes to turn. Besides upstream solutions, then, we must also incorporate downstream solutions into a three-pronged approach: reduce, re-use and recycle. By harnessing the power of the circular economy in addition to promoting more responsible consumer behaviours, we may one day be able to make plastic pollution a thing of the past.
1 Parker, L. (2018) ‘A whopping 91% of plastic isn’t recycled’, National Geographic. Available here.
2 Brooke, C. (2016) ‘Total amount of plastic on Earth now tops 5BILLION tonnes - enough to wrap the entire planet in clingfilm’, Mail Online. Available here.
3 OECD (2018) ‘Improving Plastics Management: Trends, policy responses, and the role of international co-operation and trade’. Available here.
4 Systemiq and The Pew Charitable Trusts (2020) ‘Breaking the Plastic Wave: A comprehensive assessment of pathways towards stopping ocean plastic pollution’. Available here.
5 Schneider, D. R. and Ragossnig, A. M. (2015) ‘Recycling and incineration, contradiction or coexistence?’, Waste Management & Research, vol. 33, no. 8, pp. 693–695.
6 British Plastics Federation (n.d.) Chemical Recycling 101. Available here.
7 Ritchie, H. and Roser, M. (2018) ‘Plastic Pollution’, Our World in Data. Available here.
8 Parker, L. (2018) ‘China’s ban on trash imports shifts waste crisis to Southeast Asia’, National Geographic. Available here.
9 European Commission (2020) Plastic waste shipments: new EU rules on importing and exporting plastic waste. Available here.
10 Cookson, C. (2021) ‘Policies to Modernize Plastics Recycling End 2020 on a High Note’, American Chemistry Council. Available here.
11 Oxford Martin School, University of Oxford (n.d.) The Oxford Martin Programme on the Future of Plastics. Available here.
12 Tudball, M. (2020) ‘UK Government announces plans for £200/tonne plastic tax during Budget 2020’, ICIS. Available here.
13 Carbon Tracker Initiative (2020) The Future’s Not in Plastics: Why plastics demand won’t rescue the oil sector. Available here.
Important information
This document is issued by Bank Lombard Odier & Co Ltd or an entity of the Group (hereinafter “Lombard Odier”). It is not intended for distribution, publication, or use in any jurisdiction where such distribution, publication, or use would be unlawful, nor is it aimed at any person or entity to whom it would be unlawful to address such a document. This document was not prepared by the Financial Research Department of Lombard Odier.
Read more.
share.