rethink sustainability
Decarbonising heavy industries: why this crucial transition will succeed little by little
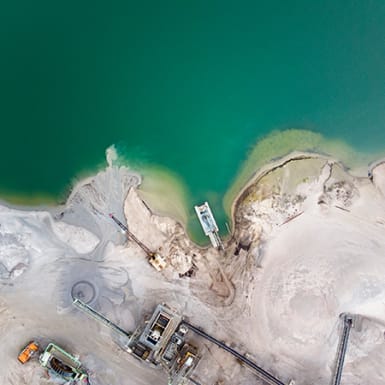
Thanks to technological advances, the steel, cement and chemicals sectors are beginning to wean themselves off fossil fuels, but it's a gradual, uphill process.
As the world targets net-zero emissions during the decades to come, some aspects of the way we live are proving easier to decarbonise than others. Among the most challenging sectors are the energy-intensive industries we rely on to produce basic materials, such as steel, petrochemicals, aluminium and cement.
Between them they are responsible for some 22 per cent of global CO2 emissions1 – a share that is likely to grow with continued demand for such products, which underpin economic development, and as other sectors decarbonise.
What makes these so-called “hard to abate” industries the awkward squad of the decarbonisation drive? The basic answer is that many of them, including steel and cement, use high-temperature processes that rely on burning cheap fossil fuels. Others emit carbon from non-energy sources. In the chemicals sector, for example, ammonia production uses natural gas as a feedstock.
“The kind of change we are talking about, to get these industries to net zero, is unprecedented,” says Chad Holliday, Co-chair at the Mission Possible Partnership, an industry group that focuses on decarbonisation of the hard-to-abate sectors. “The good news is that we now know more on how to keep the planet below 1.5 degrees and have shown radical collaboration is possible, even among competitors.”
Some experts characterise the relationship between these heavy industries and fossil fuels as a dependency; decades of development and process improvements have locked the use and emission of carbon into existing production systems. That means change is not as simple as, for example, replacing a polluting source of electricity for a renewable alternative.
Read also: Investing in the future of hydrogen
Potential for hydrogen fuel
Still, dependencies can be lifted with the right approach. And many in these heavy industries are looking at plans to reduce their carbon emissions2. A switch to hydrogen could provide a sustainable alternative, and Canada is well positioned to take advantage, with the capacity to produce low-carbon hydrogen from several sources. To truly reduce carbon emissions, so-called green hydrogen could be made by using renewable electricity to split water. Although a promising long-term solution, it could take several decades to scale up.
Carbon capture and storage technology could massively reduce greenhouse gas pollution, from both fuel and process emissions, in the hard-to-abate sectors3, assuming the costs can be brought down. Scrubbing carbon dioxide from waste and exhaust gases and squeezing it underground could be a key method for the cement industry in particular, experts in academia and industry say.
Read also: Climeworks: combatting global warming by sucking CO2 out of the air
That's because cement production includes carbon dioxide production that can't be tackled any other way – when limestone is heated to make the key ingredient, called clinker. These non-combustion emissions help explain why, if the cement industry were a country, it would be the third largest emitter in the world4. “Key for decarbonising our industry is to find, apply and scale technical solutions for carbon capture and utilisation or storage,” says Dominik von Achten, Chairman of the Managing Board of HeidelbergCement. Another way to reduce carbon emissions from cement production is to substitute the clinker for less polluting options, such as coal fly ash or blast furnace slag.
HeidelbergCement is currently building the world's first full-scale installation for carbon capture at the Brevik cement plant in Norway, capturing 400,000 tonnes annually (or 50 per cent) of the plant's emissions from 2024 onwards5. “This will be a game changer for our industry,” says von Achten.
Read also: Where biodiversity protection meets decarbonisation
Advent of the circular economy
Other strategies that can chip away at heavy-industry emissions include the idea of the circular economy, which minimises waste and embeds sustainability. This set of approaches encourages efficient use of materials through recycling, reuse and reduction of the materials along entire supply chains. The Energy Transitions Commission estimates that moving to a circular economy for plastics, steel, aluminium, and cement would reduce carbon dioxide emissions 40 per cent globally, and 56 per cent in developed economies, by 20506. This reduction relies on a two-pronged approach: making better use of existing stocks of materials through greater and better recycling and reuse and reducing the materials requirements in key value chains through improved product design, longer product lifetime, and new service-based and sharing business models.
The durability of steel, for example, lends itself to remanufacturing, which restores items such as wind turbines, engines, and electric motors to new. And a number of companies, such as the London-based Polymateria, are developing truly reusable plastics that are easier to break down and recycle.
Read also: The CLICTM Chronicles: 10 ways to build a circular economy and the companies leading the way
In some cases, the efficiency of the industrial processes themselves can be optimised. If the gains of such improvements might appear modest, they can still be significant because of the overall scale of the emissions. By using artificial intelligence to analyse manufacturing data, experts can recommend ways to cut emissions during the production of cement, steel and glass7. The tool models the production environment, and identifies the optimal process for the lowest possible carbon dioxide output and fuel use.
“We're translating AI research into gigatonnes of impact on emissions, and solving some of the biggest challenges associated with climate change,” says Aidan O'Sullivan of the company Carbon Re, which is working with cement companies. “If you do a little bit of improvement, you could get massive reductions in emissions,” he says. “Because they're such big emitters, a one per cent improvement is the same as taking a huge number of cars off the road.”
1 Bataille, C.G.F. 2019. “Physical and Policy Pathways to Net-Zero Emissions Industry.” WIREs Climate Change, December 22. https://doi.org/10.1002/wcc.633.
2 https://www.energy-transitions.org/publications/mission-possible/
3 https://globalchange.mit.edu/publication/17657
4 https://www.bbc.co.uk/news/science-environment-46455844
5 https://www.heidelbergcement.com/en/pr-02-06-2021
6 https://www.energy-transitions.org/publications/mission-possible/#:~:text=The%20report%20Mission%20Possible%3A%20Reaching,60%25%20by%20mid%2Dcentury%20as
7 https://www.ucl.ac.uk/news/2021/oct/ucl-climate-tech-spinout-uses-ai-technology-cut-industry-emissions-gigatonnes
Important information
This document is issued by Bank Lombard Odier & Co Ltd or an entity of the Group (hereinafter “Lombard Odier”). It is not intended for distribution, publication, or use in any jurisdiction where such distribution, publication, or use would be unlawful, nor is it aimed at any person or entity to whom it would be unlawful to address such a document. This document was not prepared by the Financial Research Department of Lombard Odier.
Read more.
share.