rethink sustainability
Smart containers: how Swiss company AELER is transforming the logistics industry
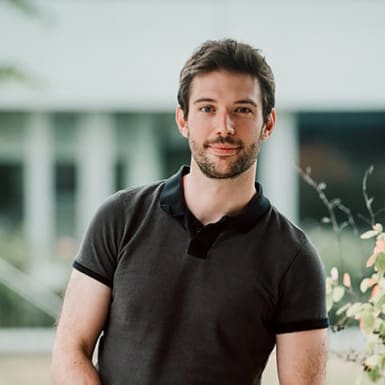
Every day, millions of tonnes of goods are moved around the world, bringing us the essentials we need to feed and clothe ourselves and the luxuries we use for relaxation and entertainment. Though this vast web of freight transportation is an essential part of international trade and our daily lives, the many kilometres travelled represent mammoth CO2 emissions. In fact, with 80% of the volume of globally traded goods being moved by sea, according to David Baur, co-founder and CEO of Swiss company AELER, “If shipping were a country, it would be the world’s sixth largest polluter.”
In this sprawling global supply chain, one of the rare common denominators is the shipping container. This large metal box, which first appeared in the 1950s, has barely evolved since the 1970s. That is precisely where AELER has set itself apart, with containers made from insulated, innovative composite materials, onboard sensors, and web connectivity that provides real-time access to a rich array of data, including GPS tracking, temperature, CO2 emissions and loading safety.
With sensors integrated into their containers right from the design stage, AELER offers data collected and displayed on a unified digital platform, allowing goods to be closely monitored along supply chains. We discovered more with David Baur, as he presented the innovation at an event organised by Lombard Odier.
Partnering with luxury brands and big pharmaceuticals
David Baur began by explaining, “There are currently just two types of container on the market, classic containers and refrigerated containers. We propose a third option, with an insulated, intelligent container, better suited to certain types of goods.”
AELER’s strategy, he noted, lay in wooing around twenty international carriers and groups – such as an American multinational, French luxury brands and big names in Swiss pharma – and targeting specific segments which account for some 20% of the world market. They include products that are sensitive to temperature but that do not actually require refrigeration – ranging from medicinal products to leather goods, and even materials for information technology. Some products, he explained, require enhanced monitoring which is enabled by connectivity, for instance some luxury items or certain liquid goods, such as skincare products and liquid raw materials.
Maintaining temperature and calculating the carbon footprint
In a standard, uninsulated, steel container, the temperature can range from below zero to above 70 degrees Celsius. Where necessary, refrigerated containers are used to protect merchandise, but they are complex and expensive. For their part, AELER guarantees a temperature of between 0 and 40 degrees as standard.
“Classic containers can be insulated using single-use plastic materials. However, not only is this practice costly and time-consuming; it is, more importantly, not sustainable,” David Baur explained. “Thanks to our insulation being integrated into the structure, it is possible to load an average additional 4 tonnes of liquid cargo per container. This increases capacity by around 23 to 27 tonnes.”
It is there that the economic benefit adds to the sustainability and technical benefits of AELER containers. This added capacity per unit makes a clear difference when multiplied on a large scale. “For the large groups we work with, it is a huge leap forward because it means they can ship the same product volume in fewer containers, thereby reducing their carbon footprint.”
Read also: the low-carbon materials that could slash construction emissions
The ability to carry greater loads also comes from the materials used to make the containers. Their advanced composite structure makes them stronger than classic containers – fewer containers means improved energy efficiency throughout the supply chain.
Sea freight instead of air freight
AELER’s innovations mean that some non-urgent products that were previously transported by air can now be shipped by sea. “We are currently seeing a tendency for companies to change the mode of transport used for certain goods, thanks to the technical specificities of our containers, because it is easier to track and trace them. So, thanks to the ‘mass’ effect of a cargo ship transporting hundreds of containers, compared to a limited plane load, the CO2 impact has been significantly slashed, by as much as 90% per trip,” David Baur explained.
Created as a lean start-up in 2018 by David Baur and Naïk Londono, both graduates of the Ecole Polytechnique Fédérale de Lausanne, AELER now has around fifty employees, and is ready to expand. “Thanks to the projects underway with large groups on certain specific products, we want to move from several hundred to several thousand containers,” David Baur said.
Based in the EPFL Innovation Park, and with production facilities sited in Eastern Europe in order to be close to the Swiss-based teams, the company says it is ready to conquer new clients and new markets. Having raised CHF 7 million in 2022, the company is in the process of raising more this year to fund its growth.
Decarbonising international transport
According to the United Nations Conference on Trade and Development (UNCTAD), ships carry over 80% of the global trade in goods by volume, mostly in shipping containers. In 2023, the 175 member states of the International Maritime Organisation (IMO), a UN agency, agreed to reduce greenhouse gas (GHG) emissions from the shipping industry by at least 70% by 2040 (compared to a 2008 baseline).
Forecasts published by the European Environment Agency indicate that shipping GHGs could reach 17% of all world emissions by 2050 if no concrete measures are taken to decarbonise the sector. Highlighting these decarbonisation commitments, David Baur noted, “We are seeing a trend in emission offsetting with carbon credits. The supply chain is complex and, despite the many initiatives and innovations, such as cleaner fuels, using them on a large scale remains a huge challenge.”
Read also: E-bikes are gearing up for growth | Lombard Odier
"We avoid using single-use plastic items for insulation and we load more per goods per container. Our sensors allow us to make real-time calculations of CO2 emissions and to use GPS tracking and tracing, thereby reducing the number of trips and the risk of loss or theft."
AELER calculates these emissions using a method developed by the Global Logistics Emissions Council (GLEC) Framework. For the big groups that AELER works with this is invaluable information, as they work to cut their carbon emissions and fine-tune their understanding of the environmental impacts of their supply chains.
While AELER makes no claim of revolutionising shipping in its entirety, for its big-name partners, the gains are tangible. As firms like AELER and numerous other start-ups strive to scale the innovations that will help us move to a sustainable economy, investors and the financial sector have a crucial role to play, funding the rollout of solutions that are helping to reduce CO2 emissions throughout the logistics value chain and across the wider economy.
Important information
This document is issued by Bank Lombard Odier & Co Ltd or an entity of the Group (hereinafter “Lombard Odier”). It is not intended for distribution, publication, or use in any jurisdiction where such distribution, publication, or use would be unlawful, nor is it aimed at any person or entity to whom it would be unlawful to address such a document. This document was not prepared by the Financial Research Department of Lombard Odier.
Read more.
share.